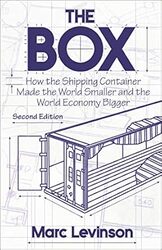
Rating: 7.9/10.
The Box: How the Shipping Container Made the World Smaller and the World Economy Bigger by Marc Levinson
Book about the history of the shipping container and how it changed global trade. The shipping container revolution began in 1956 and has made the transportation of goods across the world extremely fast and efficient, which has had wide-ranging consequences on the distribution of labor: since there is no longer as much advantage in manufacturing products locally, production has shifted to wherever labor costs are lowest.
Before the shipping container’s debut in 1956, all goods had to be loaded manually on and off ships by crews of longshoremen. This had many problems: it was an intense and unstable job requiring a lot of labor, the work and labor were inconsistent, goods were often stolen, and the process of loading and unloading cargo would eat up roughly half of the total shipping costs.
Malcolm McLean (whom the book credits largely as being responsible for much of the container revolution), started in the trucking industry, which, despite being a heavily regulated business, he was able to grow due to his financial acumen. He realized that trucks could be driven onto ships and optimized the process further by recognizing that the truck cab was not needed, then designed the containers to be easily stacked and lifted by cranes. He was able to demonstrate that this process was an order of magnitude cheaper than the status quo, thus kickstarting the revolution.
Container shipping grew in the 1950s following the success of McLean and flourished in a few places dominated by islands in the US that were subject to the Jones Act, which limited competition since only vessels manufactured in the US could carry these routes, namely between the mainland and Hawaii, and between the mainland and Puerto Rico. McLean was not alone in this business, as Matson was another earlier player focusing on the Hawaii market. McLean’s company acquired some competitors and rebranded itself as Sea-Land.
Ports were affected differently depending on how they approached the new technology. Some were eager to embrace this technology, while others were resistant to it, being afraid that it would eliminate jobs and being influenced by unions. A good case study occurred between New York and New Jersey in the 1950s – the ports of New York were in a poor state with rundown infrastructure and high congestion, adding to higher costs, and were slow to change. Their neighbors at the New Jersey Port Authority embraced containers and invested heavily in container technology and traffic. Soon after it opened, the number of dock workers’ jobs in the New York port declined sharply and was taken by New Jersey. A similar situation unfolded between Oakland and San Francisco. Essentially, containerization resulted in a smaller number of larger ports, since ships would rather make longer stops in a few ports rather than stop many times, so there would only be a small number of ports in each region as the hub for containers, and every other one would go into decline; the first movers and early adopters of container technology had an advantage here.
Unions struggled against the employers about the adoption of automation during this time, but overall, it was widely recognized that automation was inevitable, and the new machinery required fewer workers to operate. The longshoreman jobs largely disappeared and were replaced with fewer but higher-paying jobs.
The standardization process was another interesting story. Around 1958, it became apparent that different shipping companies had adopted incompatible container technologies, which would essentially eliminate any benefits of containerization. Several governmental organizations were formed to try to get everyone to agree to a standard, though this was not an easy process and required many compromises since different players had varying requirements, eg: shipping by rail and by truck had very different requirements. There was also the issue of fairly treating the early adopters who had made investments before any standardization was implemented. While the process was messy, since all parties agreed that having a standard was better than not having one, broad agreement was reached by around 1965.
Another turning point was the use of container technology in managing military logistics in Vietnam. While container technology was certainly a viable business by then, it was not yet transformational and was essentially used by only a few companies in a few regions. Vietnam had many logistical issues during the beginning of the war with unloading ships and getting supplies to the right places. In 1967, Sea-Land secured a contract to help deliver with containers, which became wildly successful. They convinced the military of the value of this technology, and they also realized the profit potential after shipping equipment from America to Vietnam – now they had empty containers returning from East Asia to America so they could move goods from Japan to the US essentially for free.
The development of container ships after the 1970s has been a story of ever-increasing sizes of ports and ships, and increasing efficiency as the container logistics industry matures. All processes have become more efficient, and non-traditional routes have been invented where, instead of sending cargo to the nearest container port, it may be more efficient to send it by train long distances across the continent. Shipping companies try to optimize for as few container ship stops as possible, since these massive ships incur a few days of delay for each stop. With just-in-time shipping, companies expect precise timelines for their logistics, where shipping is so efficient that they coordinate intermediate production outputs to be shipped from one country to the next, instead of just finished products shipped to their places of demand.
One thing that has been difficult to predict is oil prices, a trend starting in the 1970s where they increased drastically and then declined. The price of oil affects the type of ship that is best fit for the market – when oil prices are high, it is more efficient to build slower and energy-efficient ships, but when prices are low, those ships are too slow to be viable. McLean’s investment in the wrong type of ships caused it to be outcompeted, and the company went bankrupt in the 1980s.
The importance of container ports to countries’ economies has become paramount after quick and efficient shipping, which has made it no longer necessary or beneficial to co-locate steps of the production process. Manufacturing now occurs in a combination of places where labor is cheapest and efficient transportation logistics exist. Poorly developed container ports can doom entire economies; for example, many African countries have very low labor costs but remain uncompetitive because their lack of ports makes transportation costs expensive.
As container ships and ports continue increasing in size and efficiency, the trend has been difficult for industry experts and regulators to predict the direction of the industry. In fact, all of the original companies, such as Matson and McLean’s companies, have gone bankrupt since there is no early mover advantage and customers are easily willing to switch to lower-cost and faster competitors. Now the largest players like Maersk and Evergreen are latecomers with multinational entities.